LT Dichtheitsprüfung (Lecksuche)
Dichtheitsprüfung, LT, Leak Testing, Dichtigkeitsprüfung, Lecksuche, Leckage-Ortung
Dichtheitsprüfung
Die Dichtheitsprüfung (LT, Leak Testing, Dichtigkeitsprüfung, Lecksuche, Leckage-Ortung) ist ein zerstörungsfreies Prüfverfahren zum Nachweis und zur Ortung von Leckagen in Druck-und Vakuumsystemen. Das auf Dichtigkeit zu überprüfende Rohrleitungssystem wird z.B. einem Über- oder Unterdruck ausgesetzt. Im Falle einer Leckage kommt es dann zu einer Druckänderung.
Bei der „Leckage“ handelt es sich um einen Flüssigkeits- oder Gasdurchtritt durch eine Fehlstelle (Leck) in einem Bauteil (Rohrleitung, Behälter).
Ein Leck kann z.B. ein Riss, ein Durchbruch, eine Kerbe oder ein Loch sein. Durch diesen Materialfehler dringt Gas (z.B. Luft) oder Flüssigkeit (z.B. Wasser) ein oder sie tritt aus.
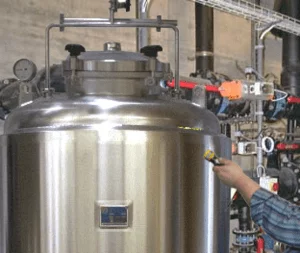
Nachweis der Behälterdekompression mit einem fluoreszierenden Konzentrat
Leckagen können die Betriebssicherheit von Vakuum- oder Drucksystemen (z.B. Druckbehälter) erheblich gefährden. Gefährliche Gase oder Flüssigkeiten können dabei austreten. In Druckluftsystemen erhöhen sich dadurch die Energiekosten merklich.
Die folgende Tabelle veranschaulicht das Verhältnis von Leckagerate, Größe des Lecks und die dadurch entstehende Leckage:
Leckagerate [m³ Pa/s] |
Durchmesser des Lecks |
Leckage durch das Leck bei Δp = 1 bar |
10¹ | 1,0 mm | Wasser läuft aus |
10-1 | 0,1 mm | Wasser tropft |
10-3 | 0,03 mm | Wasserdicht, aber gasdurchlässig |
10-5 | ≈ 3 µm | 1 Luftbläschen ( ≈ 1 mm³) in 10 Sekunden |
10-7 | ≈ 0,1 µm | ca. 1 cm³ Gasverlust in 12 Tagen |
10-9 | -- | ca. 3 cm³ Gasverlust in 1 Jahr |
10-11 | -- | ca. 1 cm³ Gasverlust in 300 Jahren |
Die Dichtheitsprüfung kann je nach zu prüfendem Bauteil mit verschiedenen Verfahren durchgeführt werden. Die „Kriterien zur Auswahl von Prüfmethoden und -verfahren“ der Dichtheitsprüfung sind in der Norm DIN EN 1779 beschrieben. Im Folgenden werden die gängigsten Verfahren kurz dargestellt:
- Blasenprüfverfahren (DIN EN 1593 "Zerstörungsfreie Prüfung - Dichtheitsprüfung - Blasenprüfverfahren")
- Abdrückverfahren
- Akustische Leckprüfverfahren
Anwendungsbereiche
Die Anwendungsbereiche sind vielfältig:
- Rohrleitungen und Behälter
- Vakuum- oder Druckgassysteme
- Hydraulik- oder Gassysteme
- Pyrotechnische Einrichtungen
- Elektronische Bauteile
- Klimaanlagen
- Lebensmittelverpackungen
Verfahren der Dichtheitsprüfung
Blasenprüfverfahren nach DIN EN 1593
DIN EN 1593 "Zerstörungsfreie Prüfung - Dichtheitsprüfung - Blasenprüfverfahren"
Das Blasenprüfverfahren (pneumatisches Verfahren) ist ein häufig eingesetztes, visuelles Dichtigkeits-Prüfverfahren. Seine Anwendung wird ausführlich in der Norm DIN EN 1593 beschrieben.
Ein Nachteil des Blasenprüfverfahrens ist, dass die Prüfoberfläche zugänglich und sichtbar sein muss. Sie sollte auch gründlich gereinigt sein, um Falschanzeigen zu vermeiden. Diese können z.B. durch Behinderung der Blasenbildung aufgrund von Oberflächenverschmutzungen auftreten.
Vorteilhaft ist, dass mit Luft als Prüfgas geprüft wird.
Die Prüfflüssigkeit ist ein schaumbildender Indikator, eine Emulsion aus Benetzungs-, Filmbildungs- und Feuchtebindungsmitteln. Zum Nachweis kleiner Leckagen wird eine gleichmäßig dünne, gut benetzende Schicht benötigt. Am Ort der Leckage kommt es dann nach Erzeugung der Druckdifferenz durch den Gasaustritt zur Blasenbildung (s. Abb. unten).
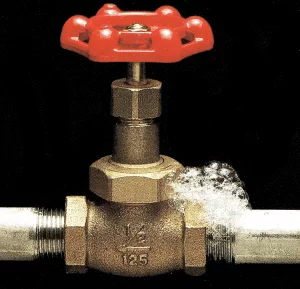
Blasenprüfverfahren unter Einsatz des HELLING Lecksuchsprays „Proof Check“
Wenn möglich, wird das Prüfobjekt in die Prüfflüssigkeit getaucht. Die Prüfflüssigkeit kann auch auf die Unterdruckseite des Prüfteils (z.B. bei einer Schweißnaht an einem Behälter) aufgetragen werden. Das zu prüfende Bauteil wird dann mit einem Überdruck beaufschlagt. Am Ort des Lecks kommt es zu einer deutlichen Schaumbildung.
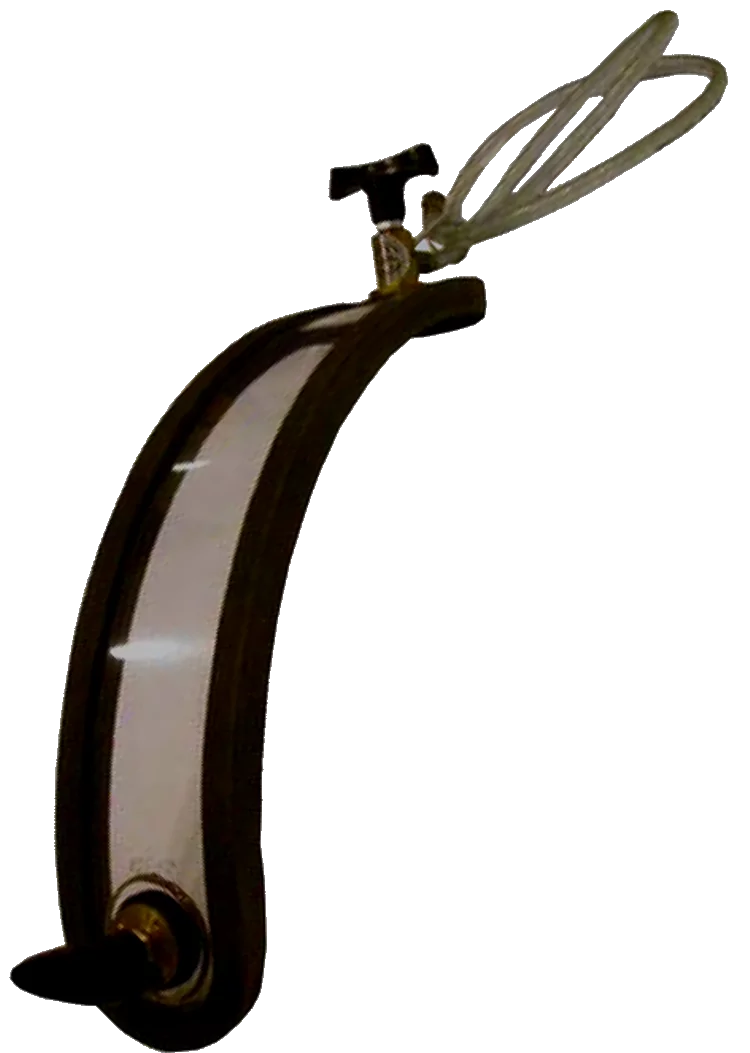
Vakuumbrille für Rundnähte mit durchsichtiger Makrolon-Scheibe. Durch die Moosgummidichtung liegt die Vakuumbrille dicht auf dem Prüfobjekt auf.
Handelt es sich bei dem Prüfobjekt um ein druckloses Bauteil, kann eine sogenannte Vakuumbrille (s. Abb. oben) eingesetzt werden. Diese gibt es in den unterschiedlichsten Ausführungen. Mit Hilfe einer entsprechenden Vakuumpumpe wird dann der erforderliche Unterdruck hergestellt.
Prüfmittel für die Lecksuche mit dem Blasenprüfverfahren
Abdrückverfahren
Beim Abdrückverfahren ist der Indikator ein farbiges (fluoreszierendes) Konzentrat auf Wasser- oder Ölbasis. Die Konzentrate beinhalten Luminophoren, Benetzungsmittel und Rostschutz.
Der Indikator wird der Prüfflüssigkeit beigemischt. Danach wird das Bauteil (z.B. eine Rohrleitung oder ein Behälter) abgedrückt. Nach einer vorgegebenen Druckhaltezeit wird die äußere Bauteiloberfläche unter UV-Bestrahlung visuell geprüft. An Orten von Leckagen tritt die Prüfflüssigkeit aus dem Bauteil aus und kann so gut detektiert werden.
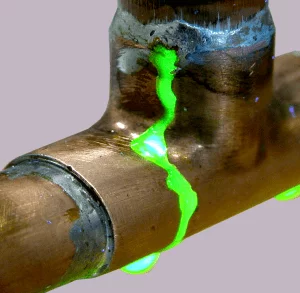
Leckageortung in einem Kühlsystem: Anwendung des Abdrückverfahrens mit farbiger fluoreszierender Indikatorflüssigkeit
Produkte für das Abdrückverfahren
Akustische Leckage-Ortung
Gase oder Flüssigkeiten, die durch ein Leck entweichen, erzeugen durch Turbulenzwirbel Ultraschallvibrationen. Diese können mit entsprechenden Ultraschalldetektoren lokalisiert werden. Dabei werden die oszillierten Vibrationen durch Signalwandler in einen niederfrequenten Schall im Hörbereich des Menschen umgewandelt.
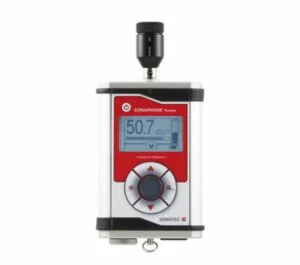
Leckage-Ortung mit einem Ultraschalldetektor. Detektion der Ultraschallvibrationen, die durch die bei Gas- oder Flüssigkeitsaustritt erzeugten Turbulenzwirbel entstehen.
Außerdem werden die detektierten Ultraschallsignale in elektrische Signale umgewandelt, die dann auf dem Display des Gerätes dargestellt werden.
Das Ermitteln von Schallsignalen bei Gas- oder Flüssigkeitslecks hat viele Vorteile gegenüber anderen Lecksuchmethoden, bei denen die Prüfoberfläche zugänglich sein muss und eine visuelle Inspektion erforderlich ist.
Ultraschallprüfgerät für die akustische Lecksuche
Welche Anforderungen werden an das Prüfpersonal gestellt ?
Für die normgerechte Durchführung von Dichtheitsprüfungen (Dichtigkeitsprüfungen) wird meist nach DIN EN ISO 9712 geschultes und zertifiziertes Stufe 1 oder Stufe 2 Prüfpersonal gefordert. Entsprechende Schulungen DIN EN ISO 9712 werden im DGZfP Ausbildungszentrum Hamburg/Helling angeboten. Das dreistufige Qualifizierungssystem unterscheidet
Stufe 1 Prüfer:
Der Stufe 1 Prüfer ist qualifiziert, ZfP-Arbeiten nach Prüfanweisung unter Aufsicht von Stufe 2 oder Stufe 3 Personal durchzuführen.
Nicht dazu gehören:
- Auswahl der Prüfverfahren und Prüftechnik
- Selbständige Bewertung der Prüfergebnisse
Stufe 2 Prüfer:
Der Stufe 2 Prüfer ist qualifiziert, zerstörungsfreie Prüfungen nach aufgestellten oder allgemein anerkannten Verfahrensweisen durchzuführen und zu leiten.
Stufe 3 Prüfer:
Der Stufe 3 Prüfer ist qualifiziert, jede ZfP-Tätigkeit zu leiten, für die der Stufe 3 Prüfer zertifiziert wurde
ZfP-Lehrgänge und weitere Informationen zur Qualifizierung und Zertifizierung von ZfP-Personal