LT Leak testing (leak detection)
Leak Testing, LT, Leak detection, Leak locating
Leak testing
Leak testing (LT) is a non-destructive test method for detecting and locating leaks in pressure and vacuum systems. For example, a piping system to be checked for leaks is subjected to positive or negative pressure. In the event of a leak, there is a change in pressure.
"Leakage" is the passage of liquid or gas through a defect (leak) in a component (pipeline, container).
A leak can be, for example, a crack, a breakthrough, a notch or a hole. Through these material defects gas (e.g. air) or liquid (e.g. water) can enter or escape.
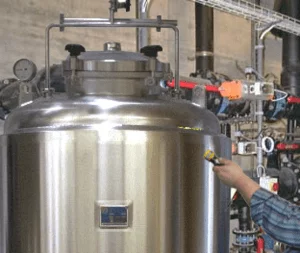
Detection of vessel decompression with a fluorescent concentrate
Leakages can significantly endanger the operational safety of vacuum or pressure systems (e.g. pressure vessels). Dangerous gases or liquids may escape. In compressed air systems, this noticeably increases the energy costs.
The following table illustrates the relationship between the leakage rate, the size of the leak and the resulting leakage:
Leakage rate [m³ Pa/s] |
Diameter of the leak |
Leakage through the leak at Δp = 1 bar |
10¹ | 1,0 mm | Water is leaking out |
10-1 | 0,1 mm | Water is dripping |
10-3 | 0,03 mm | Waterproof but gas permeable |
10-5 | ≈ 3 µm | one air bubble ( ≈ 1 mm³) in 10 seconds |
10-7 | ≈ 0,1 µm | approx. 1 cm³ gas loss in 12 days |
10-9 | -- | approx. 3 cm³ gas loss in 1 year |
10-11 | -- | approx. 1 cm³ gas loss in 300 years |
The leak test can be performed using different methods depending on the component to be tested. The "Criteria for the selection of test methods and procedures" for leak testing are described in the standard EN 1779. The most common methods are briefly described below:
- Bubble tests (DIN EN 1593 "Non-destructive testing - Leak test - Bubble test method")
- Pressure test
- Acoustic leak test methods
Application areas
The areas of application are manifold:
- Pipelines and vessels
- Vacuum or compressed gas systems
- Hydraulic or gas systems
- Pyrotechnic facilities
- Electronic components
- Air conditioners
- Food packaging
Leak testing methods
Bubble test according to EN 1593
EN 1593 "Non-destructive testing - Leak test - Bubble test method".
Thebubble test method (pneumatic methof) is a commonly used visual leak testing method. Its application is described in detail in the standard EN 1593.
A disadvantage of the bubble test method is that the test surface must be accessible and visible. It should also be thoroughly cleaned to avoid false indications. These can occur, for example, by hindering the formation of bubbles due to surface contaminations.
It is advantageous to test with air as test gas.
The test liquid is a foam-forming indicator, an emulsion of wetting, film-forming and moisture-binding agents. A uniformly thin, well-wetting layer is required to detect small leaks. After the pressure difference is generated bubbles arise by the gas leakage at the location of a leakage,(see Fig. below).
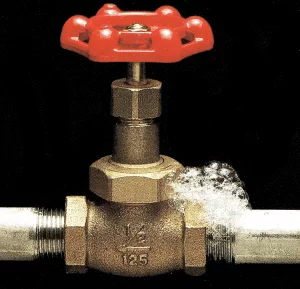
Bubble test using the HELLING "Proof Check" leak detection spray
If possible, the test object is immersed in the test liquid. The test liquid can also be applied to the vacuum side of the test object (e.g., for a weld seam on a container). The component to be tested is then subjected to an overpressure. Significant foaming occurs at the location of the leak.
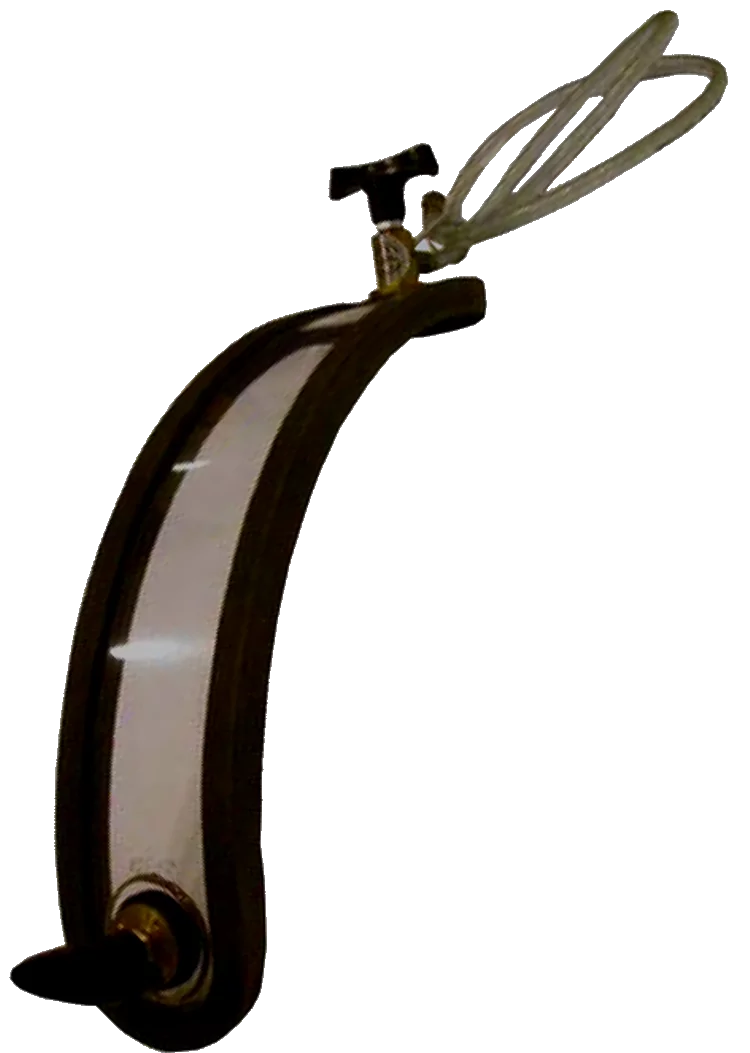
Vacuum goggles for circumferential seams with transparent Makrolon plate. Due to the sponge rubber seal, the vacuum goggles lie tightly on the test object.
If the test object is a pressureless component, a so-called vacuum gland (see figure above) can be used. These come in a wide variety of designs. The required vacuum is then created with the aid of a corresponding vacuum pump.
Test equipment for leak detection with the bubble test method
Pressure test
In the push-off method, the indicator is a colored (fluorescent) concentrate based on water or oil. The concentrates contain luminophores, wetting agents and rust inhibitors.
The indicator is added to the test liquid. After that, the component (e.g. a pipeline or a container) is pressed off. After a specified pressure holding time, the outer component surface is visually inspected under UV irradiation. At locations of leakage, the test liquid escapes from the component and can thus be easily detected.
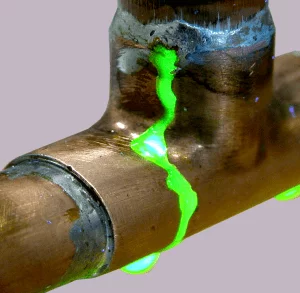
Leak detection in a cooling system: application of the bead breaking method with colored fluorescent indicator liquid
Products for the bead breaking process
Acoustic leakage detection
Gases or liquids escaping through a leak generate ultrasonic vibrations due to turbulence eddies. These can be localized with appropriate ultrasonic detectors. In this process, the oscillated vibrations are converted by signal converters into a low-frequency sound in the human hearing range.
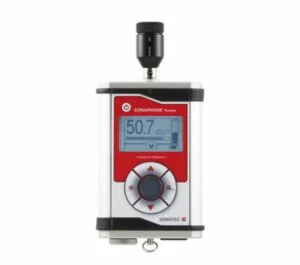
Leakage detection with an ultrasonic detector. etektion der Ultraschallvibrationen, die durch die bei Gas- oder Flüssigkeitsaustritt erzeugten Turbulenzwirbel entstehen.
In addition, the detected ultrasonic signals are converted into electrical signals, which are then shown on the display of the device.
Detecting sonic signals for gas or liquid leaks has many advantages over other leak detection methods that require access to the test surface and visual inspection.
Ultrasonic tester for acoustic leak detection
What are the requirements for the NDT personnel ?
For the standard-compliant performance of leak tests (tightness tests), level 1 or level 2 test personnel trained and certified in accordance with DIN EN ISO 9712 are usually required. Corresponding EN ISO 9712 training courses are offered at the DGZfP Training Center Hamburg/Helling. The three-stage qualification system distinguishes
Level 1 Examiner:
The Level 1 test personnel is qualified to perform NDT work according to inspection instructions under the supervision of Level 2 or Level 3 personnel.
Does not include:
- Selection of test methods and testing technology
- Independent evaluation of the test results
Level 2 Examiner:
The Level 2 Inspector is qualified to perform and direct non-destructive testing in accordance with established or generally accepted procedures.
Level 3 Examiner:
The Level 3 Examiner is qualified to conduct any NDT activity for which the Level 3 Examiner has been certified.
NDT courses and further information on qualification and certification of NDT personnel