Leak testing
Leak testing or leak detection is a non-destructive testing method for the detection and localisation of leaks in pressure and vacuum systems.
"Leakage" means liquid or gas passing through a leak regardless of its physical size. A leak can be, for example, a crack, a breach, a notch or a hole, the gas (e.g. air) or liquid (e.g. water).
Leakages can significantly endanger the operational safety of vacuum or pressure systems (e.g. pressure vessels). Dangerous gases or liquids may escape. The leak test is also carried out for pyrotechnic devices, electronic parts, air conditioning systems, food packaging, etc..

Detection of vessel decompression with fluorescent concentrate H 849
The following table illustrates the relationship between the leak rate, the size of the leak and the resulting Leakage:
Leakage rate [m³ Pa/s] |
Diameter of the leak |
Leakage through the leak at Δp = 1 bar |
10¹ | 1.0 mm | Water is leaking out |
10-1 | 0.1 mm | Water is dripping |
10-3 | 0.03 mm | Waterproof but gas permeable |
10-5 | ≈ 3 µm | 1 air bubble ( ≈1 mm³) in 10 seconds |
10-7 | ≈ 0.1 µm | approx. 1 cm³ gas loss in 12 days |
10-9 | -- | approx. 3 cm³ gas loss in 1 year |
10-11 | -- | approx. 1 cm³ gas loss in 300 years |
Bubble test
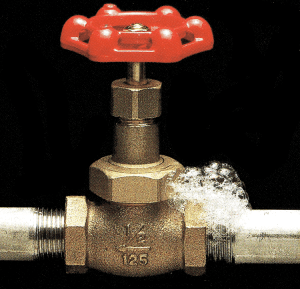
Bubble test method using the Proof Check leak detection spray
The bubble test method is a frequently used visual leak test method, i.e. the test surface must be visible.
After establishing a pressure difference at the test part, the test liquid, a foam-forming indicator, is applied to the underpressure side of the test part. A uniformly thin, well-wetting layer is required to detect small leaks. At the site of the leakage, bubbles are formed due to gas leakage.
The pressure difference can also be generated with a vacuum pump and special vacuum goggles.
This method is mainly used to find continuous leaks, e.g. in the case of
- Welded joints
- Joints or walls of systems under atmospheric pressure
- Systems that can not be squeezed off
The method can also be used to improve the sensitivity of the colour contrast penetrant testing: The area to be tested (e.g. on a weld seam) is sprayed with the leak detection spray. The transparent vacuum goggle is then put on. The space under the vacuum goggles is evacuated. Any leaks then show up as more or less large foam fungi.
Application areas
Leak testing of pressure vessels, hydraulic or gas systems.
Acoustic leak test methods
The acoustic emission leak testing method is used to find leaks in pressure or vacuum systems, e.g. for testing
- Pipelines
- Pressure vessels
- Boilers
- Manifolds
The gas or liquid flowing through the leak generates ultrasonic vibrations due to turbulence eddies, which can be localised. For this purpose, ultrasonic detectors are used to determine the vibrations oscillating in air or in the test object. Signal converters convert inaudible high-frequency sound into low-frequency sound within the range of human hearing or into electrical signals.
.Remote listening of sound signals for gas or liquid leaks often has many practical advantages over other leak detection methods. Especially when direct access to the test surface and visual inspection of the leak indications is not possible.
Pressure test

Application of the push-off method with coloured fluorescent indicator liquid
Leak testing using a coloured indicator liquid is a leak detection method similar to penetrant testing for finding material defects which are open to the surface.
In leak testing, the penetrant is applied to one side of the object wall to be tested (weld, joint). Visual inspection is performed after the specified exposure time on the other side of the wall.
The test part can also be filled with the test liquid.

Leak test on a motor vehicle engine with the fluorescent concentrate H 800
In the push-off method using an oil- or water-based fluorescent concentrate, this is added to the test liquid. The concentrates are composed of luminophores, wetting agents and rust inhibitors. After that, the system is depressurised. After a certain pressure holding time, a visual inspection of the test part surface takes place under UV irradiation. Any leaks produce brilliant fluorescent indications.
This test method is mainly used for leak testing of hydraulic systems, engines, tanks and boilers. The sensitivity of the method is about 10-5m3 Pa/s.
