PT Penetrant testing
Penetrant testing methods
PT, penetrant testing, penetration, capillary method, suction process, fluorescent and colour contrast penetrant testing.
The penetrant testing is easy to use. It is a non-destructive material testing method that does not require water or electricity. Penetrants with low surface tension and high capillary effect are used. This allows them to easily penetrate openings in the test object surface. Surface pores or fine cracks with gap widths in the µm range (≥ 25 µm) can be detected.
Typical indications that can be detected with the penetrant testing are:
- Cold cracks, hot cracks, grinding cracks
- Gas pores and clustered porosities
- Spongy texture
- Stress corrosion cracking
Depending on which penetrant is used, a distinction is made between three methods:
- Colour contrast penetrant testing (penetrant type II according to EN ISO 3452 part 1)
- Fluorescent penetrant testing (Penetrant Type I)
- Fluorescent Colour Contrast Penetrant Testing (Penetrant Type III)
Here you will find fluorescent and colour contrast penetrants, removers and developers for penetrant testing
Penetrant Testing Products Systems
The basic standard for penetrant testing EN ISO 3452 Part 1 describes in detail how to perform penetrant testing with the various testing products systems.
The testing systems for penetrant testing are classified by
- Penetrant type
- Cleaning method
- Development form
Fluorescent penetration systems are also classified according to sensitivity classes starting at ½ (insensitive) to 4 (extremely sensitive).
There are two sensitivity classes for color contrast penetration systems and fluorescent color contrast penetration systems:
Sensitivity class 1 | normal |
Sensitivity class 2 | high |
Here is an overview of the penetrant testing material according to EN ISO 3452 Part 2:
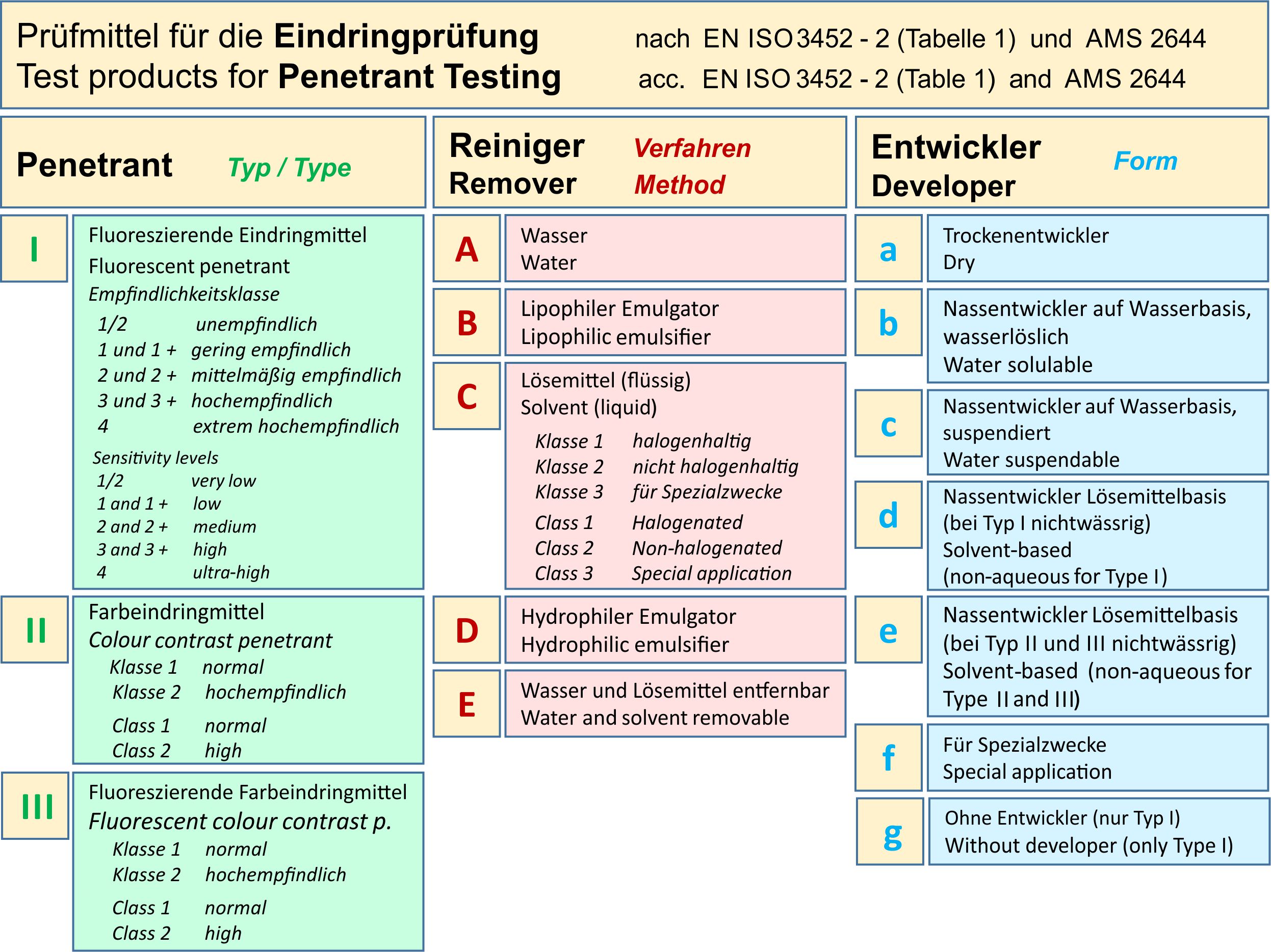
Process steps of the colour contrast penetrant testing
In the following, the essential steps in performing colour contrast penetrant testing using the red-white method are presented. A solvent-based wet developer (form e) is used.
(1) Precleaning
Mechanical precleaning - brushing, grinding, blasting
Precleaning ensures that the surface of the test object is free of contaminants. Impurities can be e.g.: rust, grease or scale. Any indications that may be present are thus made accessible for penetration by the penetrant. Precleaning can be performed:
- mechanically - e.g. brushing, grinding, blasting
- chemically by cleaning agents, whereby these must be removed from the surface after cleaning
(2) Application of the penetrant (penetration)
Penetrating - even application of the coloured (or fluorescent) penetrant.
The penetrant is sprayed onto the dry surface to be tested. The penetrant can also be applied with a brush. Or the test object is poured over with or immersed into the penetrant. In this case, the penetration time can be 5-60 minutes. This depends on the test conditions (e.g. temperature) and the test object material .
(3) Excess penetrant removal
Removal of excess penetrant, e.g. with a sponge
During excess penetrant removal, the excess penetrant is carefully removed from the test object surface after the specified penetration time. A lint-free cloth or sponge is used for this purpose. The test surface is carefully inspected for residues.
(4) Drying
Drying the test object surface with moving air
Before the developer can be applied, the test object surface must be dry (except when using a water-based developer, form b and c). This is achieved by:
- Wiping with a dry lint-free cloth
- Evaporation
- Forced ventilation (e.g. hair dryer, compressed air)
(5) Application of the developer
Uniform spraying of the white developer
The developer is applied evenly to the test object surface. A thin, homogeneous, white layer is formed. This ensures that the penetrant remaining in the surface openings is bleeding out.
(6) Inspection
Inspection of the test object surface, indications "bleed" out
Immediately after application of the developer, the test object surface is inspected according to the given inspection intervals. The required viewing conditions (see EN ISO 3059, ASTM E1417 or customer specification) are observed.
The test result and the test conditions are recorded by the NDT personnel in the test report. Depending on the test instruction or specification, documentation by fotos or video recordings are made.
PT test facilities
Installations for penetrant testing are individually developed at the HELLING Center for Technology according to the customer's specification.
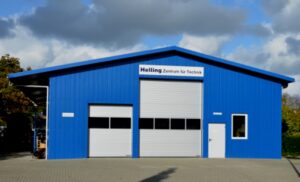
The "Blue Hall" - HELLING Center for Technology
PT test facilities are mainly made of stainless steel. Control systems are manufactured by well-known manufacturers.
A penetrant installastion is composed of the following process stations, for example:
- Pre-cleaning
- Washing
- Drying → at up to 100 °C
- Cooling → down to 40 °C
- Application of the penetrant
- Washing
- Emulsifying
- Re-washing
- Drying → at 60 °C
- Application of the developer
- Inspection
HELLING installations for penetrant testing meet the requirements of the following technical regulations:
- EN ISO 3452-1
- SAE AMS 2644
- ASTM E1417
European regulations regarding occupational health and safety, and ergonomics are of course complied with.
PT installations for penetrant testing, manufactured according to customer specifications and international technical regulations
Advantages and disadvantages of penetrant testing
The advantages of fluorescent and colour contrast penetrant testing are:
- Penetrant testing is an easy-to-use and sensitive method for in-situ surface crack testing; cracks <1 µm are detectable.
- Very wide range of application, as the application is independent of the shape and size of the test parts.
- Large areas can be checked quickly.
- Penetrant testing is well suited for both single part testing and series testing.
- The method is cost-effective (low consumption of test material, no power or water supply required).
- The test sequence can be automated.
- Quite simple training effort.
The disadvantages are:
- Only material separations open to the surface can be detected.
- The test area must be accessible.
- The test procedure is relatively time-consuming.
- A defect depth statement is not possible.
- The surface must be cleaned; galvanic and paint layers must be removed.
- PT installations represent a high investment in terms of acquisition.
What are the requirements for the NDT personnel ?
For the standard-compliant performance of penetrant testing, level 1 or level 2 NDT personnel trained and certified in accordance wih EN ISO 9712 is usually required. Corresponding EN ISO 9712 training courses are offered at the DGZfP Training Center Hamburg/Helling.
The three-level qualification system distinguishes
Level 1 Examiner:
The Level 1 test personnel is qualified to perform NDT work according to inspection instructions under the supervision of Level 2 or Level 3 personnel.
Does not include:
- Selection of test methods and testing technology
- Independent evaluation of the test results
Level 2 Examiner:
The Level 2 Inspector is qualified to perform and direct non-destructive testing in accordance with established or generally accepted procedures.
Level 3 Examiner:
The Level 3 Examiner is qualified to conduct any NDT activity for which the Level 3 Examiner has been certified.
NDT courses and further information on qualification and certification of NDT personnel